A linha de produção automática de batatas fritas é uma linha de produção contínua de grande capacidade composta por uma série de máquinas de batatas fritas em aço inoxidável. A linha de produção vai desde a lavagem da batata até a fritura e embalagem. A linha de produção automática de batatas fritas é uma linha de produção altamente automatizada. Sua produção pode chegar a 3.000 kg/h. Todas as máquinas adotam aço inoxidável e são resistentes à corrosão. Recentemente, instalamos uma linha de produção de batatas fritas de 500kg/h na Turquia.
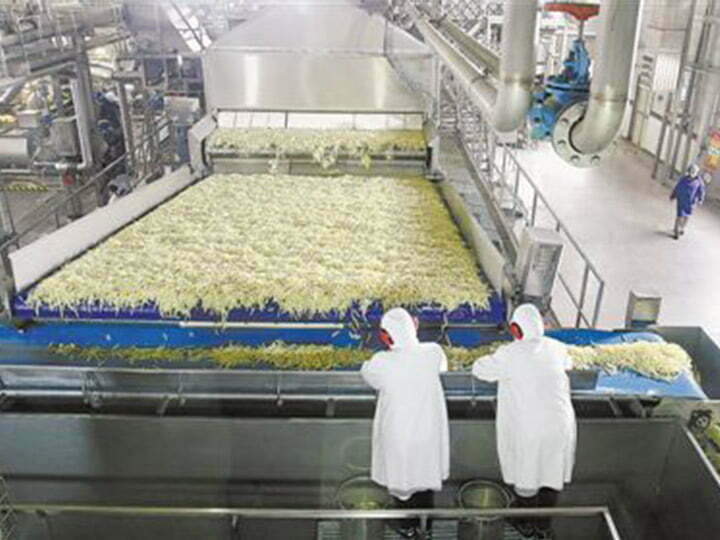
好的,我能幫你找到一些可靠的線上寫作輔導服務。你對哪種類型的寫作輔導感興趣?例如,你想提高學術寫作、商業寫作還是創意寫作?
As etapas de produção das batatas fritas incluem: lavar, descascar-cortar-branquear-desidratar-fritar-desengordurar-congelar-embalagem
Na produção de batatas fritas totalmente automáticas, todas as máquinas acima são necessárias. Além disso, também são necessários alguns transportadores para conectar duas máquinas vizinhas.
1.Lavagem e descasque de batatas. No processo de produção de batatas fritas e chips de batata totalmente automáticos, é necessário uma máquina comercial de lavagem e descasque de batatas para limpar as batatas primeiro. Ela descasca as batatas por meio do movimento de fricção reversa do rolo de cabelo e das batatas. E ao mesmo tempo, ela transporta as batatas descascadas para a saída. Sua eficiência de descasque pode atingir mais de 99%.
2.Corte de tiras de batata. A máquina de cortar batatas fritas é usada profissionalmente para cortar tiras de batata. Seu intervalo de corte é de 3-12mm. As tiras de batata cortadas têm forma regular e espessura uniforme.
3.Blanqueamento de tiras de batata. O papel do branqueamento é remover o amido das batatas para manter boa cor e sabor durante a fritura. A máquina de branqueamento contínuo de batatas atinge o objetivo de branqueamento enquanto transporta as tiras de batata.
4.Desidratação de tiras de batata. Após o branqueamento, as tiras de batata precisam ser desidratadas para uma melhor fritura. Isso também evita respingos de óleo causados por excesso de água durante a fritura. Quando as batatas branqueadas chegam à máquina desidratadora. O motor da desidratadora de vibração aciona a placa de desidratação para chocar para cima e para baixo, alcançando o objetivo de desidratação.
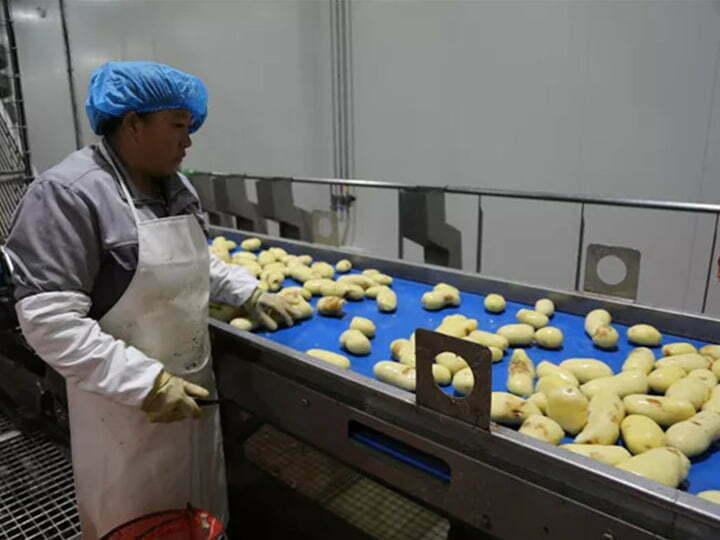
text
6.Desengorduramento de batatas fritas. Para garantir o sabor das batatas fritas fritas, é necessário usar uma máquina de desengorduramento para remover manchas de óleo excessivas na superfície das batatas fritas. O desengordurador de vibração e a desidratadora de vibração são uma única máquina. Ela adota a mesma máquina com a desidratação por vibração.
7.Congelamento de batatas fritas. É necessário para a produção em larga escala de batatas fritas ter uma máquina congeladora para congelar as batatas fritas após a fritura. Seu principal objetivo é manter as batatas fritas fritas frescas e evitar que grudem.
8.Embala de batatas fritas. Precisamos saber o tamanho e peso de embalagem exigidos pelo cliente para recomendar um modelo adequado de máquinas de embalagem. A máquina de embalagem de batatas fritas pode realizar alimentação, pesagem e selagem automaticamente. A máquina de embalagem de batatas fritas tem as características de peso de embalagem preciso e regras de selagem.

I want to improve my academic writing skills, specifically for research papers and essays. I also need help with grammar and vocabulary.
O cliente turco pretende produzir 4 toneladas de batatas fritas por dia e trabalhar 8 horas por dia. E quer investir a maior parte do dinheiro no custo de máquinas e oficinas para reduzir o uso de pessoal. E quer alcançar uma produção em larga escala e vender as batatas fritas produzidas a distribuidores locais, restaurantes e outras instituições. Por isso recomendamos a ele a linha de processamento de batatas fritas totalmente automática de 500kg/h.
Ele nos enviou para sua área de fábrica e formato, e espera que possamos orientá-lo nos desenhos da máquina e no posicionamento da máquina. Em seguida, nosso pessoal técnico negocia com os clientes o plano de colocação da máquina e envia-lhe um desenho detalhado. Após vários momentos de negociação, o cliente determinou todos os detalhes da máquina e adicionou algumas peças de reposição da máquina para sua produção posterior. Após comunicar todos os detalhes, o cliente assinou um contrato connosco.